
Basic Physics of UV Curing
In thermal drying processes, heat is used to 1) crosslink resins or 2) evaporate solvent and water-based carriers while leaving behind the residual solids. By contrast, UV curing uses the physics of light energy to initiate a chemical reaction that transforms unchained liquid-like materials into a homogeneous crosslinked solid. Uncured UV materials are composed of very tiny solid particles sometimes aided by solvent or water-based carriers.
According to the Planck-Einstein relationship,

E = Energy
h = Planck’s constant
c = Speed of light
lambda = Wavelength,
a wave’s energy (E) is inversely related to its wavelength (lambda). This means that shorter wavelengths have more energy available for harvest than longer wavelengths. Compared to infrared and visible light, UV energy is composed of much shorter wavelengths and hence, contains significantly more potential to do work.
All UV curing sources including LED, arc, microwave, and spot cure can be characterized according to spectral wavelength (nm), peak irradiance (Watts/cm2), and energy density (Joules/cm2). Understanding how these three components interact with UV formulated inks, coatings, and adhesives under specific manufacturing conditions is essential to developing and ensuring successful and controllable curing applications.
Electromagnetic Spectrum
Light exhibits properties of both particles (photons) and waves and is defined within the entire electromagnetic spectrum according to the magnitude of its wavelength. For ultraviolet energy, wavelengths are on the order of a billionth of a meter or nanometer (nm). The term ultraviolet derives from ultra which is an adjective meaning very or extremely and violet which refers to the color of the shortest portion of the visible spectrum. The category of light classified as ultraviolet is the bandwidth adjacent to (left of) the violet end of the visible spectrum as shown in the following spectral chart. UV wavelengths are just beyond those that are visible to the human eye.

Similar to the names that have been created to describe wavelengths of visible light such as red and green, there are five loosely defined bandwidths for UV, four of which are used in graphic and industrial curing. While UV bandwidths were originally developed for the medical community with segmentation based on how the different wavelengths adversely affect the human body, they were later adopted by the radiation curing industry. It should be noted that there is no official demarcation between the UV bands, and different organizations and meters will often use slightly different ranges.
-
UVA is the portion of the electromagnetic spectrum between 315 and 400 nm. UVA represents the largest portion of UV curable energy and is commonly referred to as long UV since it represents the longer wavelengths in the UV bandwidth. These longer UVA wavelengths penetrate deeper into formulations than shorter UV bands. Broadband mercury UV sources emit a peak UVA output at 365 nm while UV LEDs peak at 365, 385, and 395 nm. Medically, UVA is most responsible for skin aging and increases in skin pigmentation, and it is at the lower limit of sensitivity to the human eye.
-
UVB is the portion of the electromagnetic spectrum between 280 and 315 nm. UVB wavelengths generally penetrate just below the cure surface of formulations. Biologically, UVB is most responsible for reddening and burning of skin and vision damage. Care should be exercised in using broadband curing sources as UVB is invisible to the human eye.
-
UVC is the portion of the electromagnetic spectrum between 200 and 280 nm. UVC is commonly referred to as short UV. It is invisible to the human eye so vision protection should always be used with broadband curing sources. UVC is the primary wavelength used for surface cure. UVC, particularly 254 nm, is essential for ensuring surface hardness and texture as well as providing the scratch, chemical, and stain resistance required for many top coats. UVC includes wavelengths between 200 and 240 nm which are responsible for ozone generation. For more on ozone, refer to UV Curing Sources.
-
UVV is the portion of the electromagnetic spectrum between 400 and 445 nm. The V stands for visible since these wavelengths are visible to the human eye and overlap a small portion of the visible spectrum. While UVV rays penetrate deep into formulations, they are also plentiful in natural and artificial lighting. This can be problematic as it is difficult to prevent formulations that react in this range from curing in open containers, on equipment and other unwanted surfaces, and at dispensing points. As a result, most formulations are intentionally designed not to react to UVV.
-
vacuum UV is the portion of the electromagnetic spectrum between 100 and 200 nm. It is not a factor in curing applications as these wavelengths only travel through a vacuum and do not travel through air.
In general, longer UVA and UVV wavelengths penetrate deep into inks, coatings, and adhesives while shorter UVC wavelengths activate the surface chemistry. Providing a suitable wavelength alone, however, does not guarantee cure. The nature of the formulation, the power of the lamp, as well as other factors affect how and where UV energy is absorbed throughout the film thickness and how much crosslinking occurs.
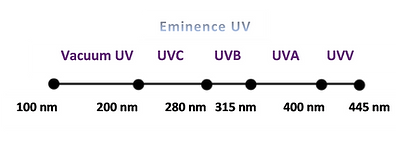

While conventional broadband UV sources such as microwave and electrode arc lamps emit UVA, UVB, UVC, and UVV as well as infrared, commercially available LED curing sources emit narrow bands of UVA closer to the visible (365, 385, 395, and 405 nm). As a result, conventional UV chemistry generally does not cure with UV LEDs and must be reformulated to cure with only longer wavelengths. Fortunately, ink, coating, and adhesive companies are increasingly designing UV LED chemistry such that a single formulation can be cured with both LED and conventional lamps. Over the coming years, more and more formulations will shift to this dual cure capability.
The following illustration overlaps the spectral output of a typical broadband mercury lamp (noted by the blue shaded area) with the four spectral peaks of commercially available UV LEDs (noted by the purple bell curves). One unique characteristic of UV LED technology is that while wavelength options are currently limited to 365, 385, 395, and 405 nm, there is an incredibly wide range of peak irradiance offerings available within those wavelengths. Systems can be supplied in mWatts/cm2 up to 50 Watts/cm2 and are typically adjustable from 1 to 10% through 100% of the maximum output. Using a UV LED system with the highest available irradiance is not always necessary as irradiance is application dependent and too high of an irradiance can diminish crosslinking and even fry some formulations. That said, the UV LED irradiance required by photopolymer chemistry is typically greater than what is required with conventional mercury systems. For more information see UV Curing Sources and UV Curing Applications.
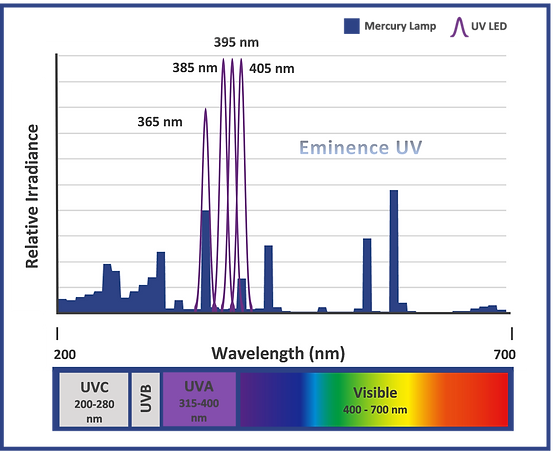
Irradiance (W/cm2)
Irradiance (Watts/cm2) is the radiant power arriving at a surface per unit area. Along with wavelength, irradiance is instrumental in light's ability to penetrate through an ink, coating, or adhesive. For UV LEDs, higher irradiance values have also been shown to aide surface cure which can sometimes compensate for the lack of UVC. It should be noted that the industry frequently uses intensity interchangeably with irradiance. While the two terms technically have different meanings, irradiance being the preferred term, the use of intensity is common and generally accepted.
While delivered irradiance often varies slightly across a cure surface, it is typically reported as the highest measured peak value. It is affected by the driven output of the engineered light source, the use and cleanliness of reflectors or optics to concentrate or contain the rays in a tighter surface impact area, and the distance the light has traveled with respect to the source or focal length.
The irradiance on a given cure surface decreases with the square of the distance from the origination source. In physics, this is known as the inverse-square law. Loosely translated it means that as UV rays travel further from their effective origin, they spread or diverge from one another which results in reduced energy concentration over a defined area at greater distances. For LEDs, the point of origin is either 1) the raw diodes (effectively the emitting window) or 2) the point at which the columnated light (when optics or reflectors are used) begins to diverge from its optical containment. For arc or microwave systems, the source is the external focal point (focused systems).
Conventional arc lamps typically emit in the range of 1 to 3 Watts/cm2 at the focus while microwave lamps generally emit as much as 5 Watts/cm2 at the focus. While it varies by system, the focal location is typically 2" from the surface of the lamp head. UV LED curing systems currently emit up to 20 Watts/cm2 at the emitting window for air-cooled heads and up to 50 Watts/cm2 at the emitting window for liquid-cooled heads. Unlike conventional lamps, UV LED systems are not typically designed to have a focus.
Inks, coatings, and adhesives require a minimum threshold of irradiance for optimal crosslinking. The industry has really never studied whether maximum threshold irradiance is something that matters, though UV LEDs seem to have already exceeded or are quickly approaching an upper limit for optimal cure in many graphical ink and coating applications. Many industrial coating applications still need to be developed for UV LED. As a result, desired irradiance for these applications is yet to be determined.
While conventional lamps typically specify their peak irradiance at the focus, there is no generally accepted standard reference for LEDs. Some suppliers specify near the diodes, others at the emitting window, and others at an offset distance from the window. In some cases the reported values are measured while in others they are theoretical. All measured values should reference the meter used and the conditions of measurement should be specified. For more information, see UV Measurement. Regardless of curing system, what is actually important is the irradiance value at the cure surface. Unfortunately, not all spec sheets specify the irradiance at varying distances, and it may be necessary to ask the supplier or measure yourself.
Today, UV LED systems can be designed with irradiance levels over 10 times greater than those for conventional UV systems. New research is revealing that sometimes too high of an irradiance can result in diminishing cure as too many polymeric chains start reacting at the same time and ultimately terminate prematurely. There is an irradiance process window that should be defined for each application. It is not narrow, but there is likely both a minimum and a maximum limit for most formulations.
Energy Density (J/cm2)
Energy density (Joules/cm2) is the radiant energy arriving at a surface per unit area, and a sufficient amount is absolutely necessary for full cure. Both irradiance and energy density are important aspects of a process window. In distinguishing between the two, peak irradiance is the delivered power, and energy density is the total delivered energy. In mathematical terms, energy density is the integral of irradiance over time as illustrated by the area under the irradiance profile in the following chart.

It is possible to have two UV systems deliver the same energy density albeit at different peak irradiance levels as shown in the next chart. Both the purple and green irradiance profiles have the exact same energy density or area under the curve. One is not necessarily better than the other, but they are notably different, and chemistry will generally prefer one configuration over the other for optimal cure. Chemistry and applications must be matched to the UV output and source. Always going with the higher irradiance value without considering the role of energy density is not the path to optimal performance. Instead, it is simply maximizing one out of a number of variables that influence cure.

While technically incorrect, the industry often refers to energy density as dose, and the two words are generally accepted to mean the same. For clarification, despite being treated by the industry as synonyms, energy density actually refers to delivered energy while dose refers to the absorbed energy, which is difficult to quantify in practice.
It is important to emphasize that for a given lamp output, peak irradiance remains constant with changes in press speed while the effective delivered energy density decreases as press speeds are increased due to the media’s or part's shortened exposure time to the UV source. Energy density is a factor of the output of the engineered light source, the number of UV sources, and the exposure time or press speed. In other words, increasing the irradiance, slowing the line speed, or adding more lamps or wider lamps in the case of LEDs will all increase energy density for a given source.
Not all UV LED products with the same reported irradiance deliver the same energy density and, therefore, do not perform similarly in practice. This means that maximum line speed and proper cure may be limited for systems with less energy density. The lack of reported energy density is the single biggest factor that makes it difficult to compare commercial UV LED curing systems and match the optimal device to the application. Conversely, there has always been much less variation in output across conventional mercury UV systems with the same irradiance.
Process Window
Inks, coatings, and adhesives are formulated to react to a given UV LED output under a specific set of process conditions. For each application and formulation, there is a UV process window within which acceptable cure can be achieved. This window is not narrow, but there is an optimal set of wavelengths as well as a minimum and maximum irradiance and energy density combination that results in proper cure. Consistently operating within this window better ensures optimal line speed, a non-tacky surface, adequate adhesion, sufficient cure, minimal post cure migration, and product life among other desired performance criteria. Establishing and maintaining a UV process window for a given application is important for producing optimal yields and quality product over time. For more information see UV Measurement.
UV technology performs well when UV output is correctly matched to the needs of the application and paired with a suitably formulated ink, coating, or adhesive. Unfortunately, there is no universal UV system or process window that works equally well for all applications. The UV solution and its output should be chosen for the formulation, the plant or shop environment, the intended application, and the configuration and speed of the material handling system.
A major benefit of UV LED technology is that the discrete nature of LEDs allows for a much wider range of curing system designs that can better fit the needs of each unique application. This allows both form factor and UV output to be tailored to the respective markets and applications resulting in much more efficient and economical UV LED curing solutions compared to conventional curing technology.
Basic Chemistry of UV Curing
Inks, coatings, and adhesives are used in the fabrication, decoration, and performance enhancement of everyday products from smart phones to automobiles and from labels and packaging to wood flooring. They are applied, most often in liquid-like form, to metal, plastic, wood, paper, and other materials and then dried or cured to produce the desired final properties. In automotive and wood finishing, liquid paint sprayed onto trim and molding parts remains wet, tacky, sticky, or soft until passed through an oven. In printing presses, inks and coatings are easily smudged or smeared until fully dry. For many years, drying or curing these kinds of materials required thermal energy applied over a sufficient period of time. Convection ovens, hot air dryers, and infrared lamps have long been common drying tools in thermal manufacturing processes.
By nature, the mechanisms responsible for thermal drying and curing are frequently very slow processes, consume lots of energy, and often take up considerable space. Drying requires the evaporation of solvents, water, or other carriers, and curing relies on heat to trigger thermally activated chemical crosslinking within the material. While the means are different, the result is the same; low viscosity materials are converted into a more viscous and typically solid form.
Around the middle of the 20th century, the introduction of ultraviolet (UV) light curing began to change how manufacturers approached curing inks, coatings, and adhesives. With UV curing, exposing specially formulated materials to ultraviolet light, rather than radiated heat, triggers a very rapid chemical reaction that produces similar results to thermal curing but with less time, less scrap, less space, less heat, and often less overall cost.
UV curing requires a combination of both the right chemistry (free radical or cationic) and the right light source (arc, microwave, LED, or spot). The light source must also provide the spectral distribution (nm), irradiance (W/cm2) and energy density (J/cm2) required by the formulation. The curing process takes place over three stages: initiation, propagation, and termination.
Free Radical Curing
Free radical curing requires the use of photoinitiators in the formulations. During initiation, photoinitiators undergo a molecular change when exposed to light. Most frequently this change involves an atom or two being knocked-off, or cleaved, from the original photoinitiator molecule. Cleavage results in a new, highly reactive molecule with an unpaired valence electron. This newly created molecule is referred to as a free radical. During propagation, free radicals combine with short to medium sized monomers and oligomers in the mixture and cause chains to link together rapidly to form longer chained polymers. The reaction eventually stops when the long polymer chains reach termination producing the final, cured material. The entire process, referred to as free radical polymerization, is extremely fast and often produces full cure in a fraction of a second.
As free radicals are created, they combine with monomers and oligomers during propagation, creating longer chains and new free radicals. While this is happening, it is possible for oxygen molecules that are present in the surrounding air to combine with intermediary chains. This reduces the number of free radicals and ultimately stops further crosslinking altogether (quenching) or weakens crosslinking (scavenging). This premature halt or termination in the crosslinking process brought on by oxygen interfering with free radical polymerization is referred to as oxygen inhibition. The outcome of oxygen inhibition is that full polymerization, particularly near the top surface layer which is directly exposed to air, is incomplete. The resulting shorter chains are not as hard and may even feel sticky or tacky. Counter to intuition, the material below the top layer may be completely cured. Thinner materials are typically more susceptible to oxygen inhibition than thicker materials as the volume of material exposed to air at the top surface layer represents a larger portion of the total film volume.
With conventional broadspectra curing systems such as arc and microwave lamps, oxygen inhibition is rarely a problem. This is because the shorter UVC wavelengths, which do not penetrate as deeply into the material, are more effective at rapid polymerization at the surface, essentially beating oxygen to the punch. However, if the UV source is either too low in irradiance or dominated by longer wavelengths, which tend to be less effective at surface curing, or for very thin formulations, oxygen inhibition can still be a battle.
A common counterattack to oxygen inhibition is to eliminate oxygen altogether. This means curing in an environment void of air which is accomplished by replacing air with a different, non-reactive gas such as nitrogen. Nitrogen inerting has been a trick for solving oxygen inhibition for decades. This method is particularly attractive when a small volume of space can be maintained between the part surface and light source such as in printing or coating flat products, webs, or fiber optics.
In early work with UV LEDs, which had low irradiance, low energy density, and a relatively monochromatic spectral output near 395 nm, oxygen inhibition was a challenge. Over the years, UV LED light sources have become more powerful, and while the LED still does not have the shorter wavelengths optimal for surface curing, a bigger hammer has proven helpful by providing more rapid curing in general. At the same time, formulating specifically to the uniqueness of LED output has led to improved photoinitiator blends and new additives which react more quickly to longer wavelengths.
Another characteristic of free radical polymerization is that the ink, coating, or adhesive must be directly exposed to UV light for a sufficient period of time to complete the photochemical reaction. There must be line-of-sight between every facet of the surface and the UV light source. Shadowed areas do not cure. Once the UV source is removed, free radical generation ceases and no further crosslinking occurs.
Cationic Curing
While free radical polymerization is the most popular UV curing mechanism, a second type of UV reaction called cationic curing is sometimes used. The main differences are in the types of resins used, the initiation catalyst, and the time needed for termination.
Epoxy resins are used in cationic formulations; whereas, acrylate resins are used in free radical formulations. Unlike the free radical mechanism, cationic chemistries continue to crosslink even after the UV source is removed and until the formulation is completely polymerized. It is sometimes loosely referred to as curing in the dark. Cationic curing can be thought of as a chemical game of dominoes—once you tip the first domino, the rest will follow, essentially assuring full cure.
Depending on the nature of the application, the proper choice of cationic or free radical chemistry depends on the comparative advantages and disadvantages of each option. On the positive side, because cationic cure is always complete, there is less of a safety concerns with residual migration. Cationic materials also adhere very well to an extremely wide range of substrates including foils and plastic films. In general, cationic cure requires less energy to initiate the reaction than free radical systems. Cationic curing also solves the problem of oxygen inhibition since oxygen does not interfere with the polymerization of cationic chemistries.
On the flip side, the acidic nature of cationic chemistry can adversely impact material delivery systems and application equipment, and the presence of high levels of moisture or high humidity in the surrounding environment can be problematic. Water reacts with the cation intermediary to halt polymerization. Cationic polymerization also takes more time than free radical polymerization and may not be fast enough for some high-speed production lines. For some jobs, like inkjet printing, the domino effect may actually present a formidable challenge when it comes to producing a cationic system that does not initiate curing until after jetting or damage the print heads and fluid delivery system. The right chemistry choice is usually very application dependent.
Raw Materials
UV chemists are similar to great chefs. A successful recipe depends on understanding how to select the right ingredients and how to mix them in just the right proportions. A dash of this or that can mean the difference between mediocre and superior results. A good cook may not manufacture the spices used, but they understand what is available and how each component balances every other ingredient.
UV inks, coatings and adhesives span a wide range of chemistries and applications, but all of the formulations draw from a common set of building blocks including oligomers, monomers, photoinitiators, additives, and pigments. Below is a simplified illustration of the raw materials used in UV chemistry along with respective proportions.

The choice of oligomers, monomers, and reactive diluents (thinners) is of major importance to the design of UV materials. These ingredients make up the largest portions of the final product. Within free radical curing systems, most of the UV formulations designed for substrates ranging from paper and wood to plastics and glass are based on acrylate polymer chemistry. Acrylate polymers are plastics with inherent properties of transparency, resistance to breakage, and elasticity. The flexibility of these acrylate systems provides formulators with an extensive choice of ingredients making it easier to select materials that will give both the desired functional performance and cosmetic appearance.
Oligomers
Oligomers can be compared with the resin in conventional material formulations. The selection of oligomers, which are typically the most abundant component by weight in a formulation, is a critical decision that has a major impact on performance. Some of the important characteristics provided by oligomers are:
-
Reactivity
-
Adhesion
-
Gloss
-
Yellowing
-
Scratch resistance
-
Chemical resistance
Very often a combination of these various properties is required while simultaneously meeting defined cost targets. Formulators often choose from a selection of oligomers that have very different chemical structures, and the best choice is frequently based on considerations such as the chemical family of the oligomers as well as the respective functionality and molecular weight.
The most popular oligomer families are:
-
Epoxy acrylates
-
Urethane acrylates
-
Polyester acrylates
-
Polyether acrylates
-
Acrylic acrylates
Monomers and Reactive Diluents
Very short chain, low molecular weight monomers are frequently used as reactive diluents or thinners in UV formulations. Sometimes large volumes of monomers are used in formulations, particularly when low viscosity is desired. This means that the impact of monomer selection can be quite significant. In addition to acting as reactive diluents, monomers are also responsible for properties such as reactivity, adhesion, and chemical and scratch resistance.
There is a rather large selection of monomers from which to choose, and four broad parameters span the available choices.
-
Functionality
-
Chemical backbone
-
Chemical structure
-
Molecular weight
Functionality
In general, the greater a monomer’s functionality, the greater its chemical reactivity. This makes sense since higher functionality means that more acrylate double bonds are available for crosslinking. On the other hand, with lower functionality comes lower viscosity. As a result, mono-functional monomers make great reactive diluents, di-functional monomers are good reactive diluents, tri-functional monomers are fair reactive diluents and multi-functional monomers produce poor reactive diluents. Another consequence of functionality is shrinkage during polymerization. Because of this, lower functional monomers are most often chosen to improve adhesion to more difficult substrates.
Chemical Backbone
Two major monomer chemical backbones are:
-
Hydrocarbons
-
Ethers
Hydrocarbon monomers have lower surface tensions desirable for substrate wetting when improved adhesion is required. These monomers also tend to have excellent flexibility, provide weatherability, and are less prone to yellowing. Since hydrocarbons are known to be hydrophobic, they also have excellent water resistance. Ether backbone monomers are more polar than hydrocarbons and are often chosen as reactive diluents. Ethers are more reactive than hydrocarbons but do not weather as well and tend to yellow more.
Chemical Structure
Monomers fall into three general structural classifications: branched, cyclic, and linear. A monomer’s structure affects the monomers glass transition temperature (called the Tg) which is responsible for rheological properties like plasticity and flexibility. Usually linear and branched monomers have lower glass transition temperatures than cyclic type monomers.
Molecular Weight
Another important property of monomers is the molecular weight. Generally speaking, a lower molecular weight produces lower viscosity and higher reactivity. Since both the chemical back-bone and the functionality effect the molecular weight, these three choices interact and often formulators need to strike the right balance.
Photoinitiators
Of all the ingredients in a UV formulation, the photoinitiator is most unique to UV curing. Photoinitiators create the magic of UV curing, harnessing light energy to create a new chemical species. The light emitted from a UV source causes the photoinitiator to fragment into reactive species. These fragments trigger rapid polymerization of monomers and oligomers to produce a highly crosslinked, durable polymer or plastic.
Since a photoinitiator’s ultimate action is dependent on its ability to absorb UV energy, each photoinitiator has a defined absorption spectra. Its reaction is triggered by light of a particular wavelength range. While this range is not narrow, it is generally optimized for either shorter or longer wavelength light sources. Choosing a photoinitiator/light source combination whose absorption and transmission profiles are compatible is essential to proper curing.
Aside from the right wavelength match, the optimal photoinitiator (or combination of photoinitiators) for an application often depends on a number of variables. These variables guide formulators in selecting which photoinitiator(s) should be chosen for a particular application and include:
-
Resin system chemistry
-
Material thickness
-
Through cure versus surface cure
-
Monomer selection
-
Process speed
-
Cosmetic and functional requirements
There are two main classes of free radical photoinitiators referred to as Type I and Type II. Type I photoinitiators are those that undergo cleavage when irradiated; whereas, Type II photoinitiators form an excited species when exposed to UV. The excited species abstracts an electron or atom from a synergist or donor molecule. Following abstraction, the donor molecule serves as the initiator for crosslinking. Phosphine oxides, aminoacetophenones, and hydroxyketones are common Type I photoinitiators. Thioxanthones and benzophenone are Type II photoinitiators.
For cationic curing, the disassociation of a salt molecule, typically a sulfonium or iodonium salt produces a reactive species. This reactive species opens an epoxy ring structure to produce polymerization.
For coatings, hydroxyketones (such as AHK) are often selected for curing pigmented or clear coatings and as one of several photoinitiators when curing the surface of highly pigmented coatings. For deeper, through cure or highly pigmented systems, a Bis-Acyl-Phosphine Oxide (BAPO) type photoinitiator is often chosen. BAPO photoinitiators are activated by longer wavelength UV and visible light. These wavelengths tend to penetrate more deeply into the coating or ink, enabling better through curing.
With UV cured adhesives and laminates, the adhesive film is often relatively thick and requires longer exposure times and more energy density in order to achieve acceptable through cure. The photoinitiator selection must be carefully considered to meet the cure performance needs of the application.
When designing a photoinitiator package, it is important to optimize the concentration of each photoinitiator in the blend. Too high a concentration of photoinitiators can cause as many problems as not having enough. For example, high levels of surface crosslinking may not allow enough UV light to penetrate lower layers. While it varies by formulation and application, photoinitiator concentrations can range anywhere from 2 to 12% by weight. A formulation can be made hotter with higher concentrations, but this can also make the formulation too reactive to be handled easily. Like the chef, the formulator creates a blend that produces a balance of effective surface and through cure coupled with the ability to cure thick and pigmented formulations when needed at a price point that is acceptable within the market.
Additives
Beyond the simple building blocks of monomers, oligomers, and photoinitiators is a deep pantry filled with other important ingredients such as pigments, flow modifiers, defoamers, dispersants, and light stabilizers. The function of an additive is to provide some kind of value added feature from a smoother finish or lower gloss to reducing foaming during mixing. Many of these additives, used sparingly, tweak the properties of a formulation just enough to make the difference between a good formulation and one that exceeds specifications.
For many UV applications that use conventional light sources, there is enough standardization that off-the-shelf products generally exist. In fact, there is an abundant choice of UV cure adhesives, inks, and coatings that work well with mercury lights sources. But change the light source or bulb, and you run the risk that standard materials won’t behave the same way. Sometimes only a small change in chemistry is needed, and sometimes it requires a deeper overhaul. While UV LED chemistry has been evolving since the mid-2000s, not all formulations exist for LED today. That said, the list is growing rapidly, the performance of both the chemistry and the light sources are improving, and demand is increasing.
Process of UV Curing
UV curing is typically just one step in a sequence of many inter-related manufacturing processes. Sometimes it is necessary to clean or surface treat the part or material before applying the formulation and then curing. It is also critical to orient the light sources as well as determine the optimal length or configuration based on the part geometry or transfer mechanism. Accessibility to the press as well as the UV source must be considered during bracket design. Shielding and safety interlocks are also vitally important to protect operators and others working near the line and prevent uncured product from continuing downstream.
Part Design
The most popular free radical curing scheme requires direct line-of-sight between the UV material and the light source. This is straightforward for roll-to-roll web processing, sheet fed applications, and parts with relatively flat surfaces or simple geometric shapes. For large or complex part profiles and assemblies, achieving line-of-sight may not be as easy to accomplish. Without direct exposure to the light source, any unexposed nook or cranny will simply not cure.
A careful consideration of UV curing should begin by reviewing all candidate parts with particular attention to size and shape in order to identify potential line-of-sight problems. The good news is that even challenging parts can often be successfully cured with good planning, proper design, and innovative thinking. Frequently the solution involves adding an extra light source or repositioning lamps for a problematic part. The part can also be positioned and sometimes moved or rotated beneath the lamps. Alternatively the lamp itself can be repositioned. Because of the more compact size and simple interconnections, repositioning an air-cooled UV LED source or liquid-cooled LED source with quick disconnects can often be a simpler task than with traditional mercury lamps where high voltage cables and exhaust ducting can make this cumbersome.
Part Handling - Web and Conveyance Mechanisms
While it is difficult to generalize about the myriad of possibilities for part handling and conveyance, a little guidance about how UV affects these choices may be useful. Since most UV materials will not cure until exposed to light, any material that is unintentionally applied to a part’s surface needs to be considered. Conveyor belts, fixtures and other hardware often get unintentionally coated, sprayed, or misted and can remain a sticky source of potential contamination. Extraneous material should be removed or cured quickly. Sometimes a light source is installed just to cure excess material from equipment surfaces.
-
Line-of-sight between the part and light source dictates the way parts need to be handled.
-
Avoiding shadow areas and presenting parts in a consistent fashion are important design considerations. Sometimes this means paying special attention to the leading or trailing edges of parts as they move past UV lamps.
-
Adding an extra lamp or two is always an option for improving exposure, but a clever design that moves the lamp or parts is sometimes more cost efficient and requires less maintenance.
Pretreatment
Without a clean surface, many final properties can be compromised such as a smooth appearance, adhesion, or corrosion protection. Even a perfectly clean surface may need to be modified to increase its surface energy so that it readily accepts an ink or coating. In order to differentiate between the two, cleaning requires pretreatment and substrate modification requires surface treatment. Frequently the two go hand-in-hand. For instance, plasma treating a plastic part both removes contaminants and modifies the surface energy of the material itself.
The selection of a proper pretreatment or surface treatment method depends on two things: the type of substrate and the nature of the contamination. Some soils are removed chemically, some mechanically, and others require treatment with flame, corona or plasma.
For removing soils, mold release agents, and other chemicals, pretreatment chemistry depends on the specific chemical nature of the soil and often the best or only way to select the most effective cleaner is by field testing.
For plastics, including many films and rigid containers, treatment of the surface with plasma, corona, or flame imparts oxygen to the molecular layers of the substrate’s surface and increases the surface energy of the treated material. Increasing the surface energy improves the wettability and provides an improved and consistent surface for further processing to occur, such as painting, printing, bonding, or laminating.
Many plastics and paper substrates are also prone to static charging, especially during processing when they pass through equipment and rollers at high speed. Statically charged parts attract dust and dirt particles. One method for reducing contamination is to neutralize the static charge using ionized air. Lightweight destaticizing guns or fixed air nozzles provide rapid static dissipation using both positively and negatively charged air to neutralize static charge and blow off surface contaminants. Guarding against static can also be as simple as stringing anti-static tinsel on the line.
Flash Time
Some UV materials require a brief time period between application and curing to allow volatile materials or carriers to evaporate. Sometimes this flash can be accelerated with low-temperature heating. Generally speaking, applying some heat to the material improves the curing characteristics. But the effects of time and temperature on applied UV materials should be verified through process testing with the material supplier.
Application Process
Before it can be cured, the UV material must be applied. Once again, there are many application variations that include adhesive dispensing, spray and curtain coating, jetting, screening, sputtering, and transfer of inks including screen, flexo, gravure, offset, digital inkjet, and pad.
Regardless of the application device, it is always prudent to safeguard against unintended exposure to UV light during the application process. Stray light from UV lamps located in close proximity to the applicator can cure materials prematurely, create contamination, and plug up the orifices of the applicator itself. Take care to isolate the application process from the curing process with appropriate shielding or profile openings.
Reclaiming UV Material
Although the applied costs of UV can be very efficient, the material itself is still a production cost. Optimizing the transfer efficiency or percent of material can make a difference in profitability. Some material inevitably ends up elsewhere and many users are motivated to collect this material and reclaim it, particularly in spray as well as curtain and flow coating applications. For many waterborne and high solids applications, this may be possible. Specially designed spray booths and chambers allow material to be channeled to a reclaim system. However, reconstituting the material can be tricky, and removing dirt and contaminants from cosmetic coatings is also necessary.
Safety Interlocks
The UV system should always be interlocked with other upstream or downstream processes so that the light source is turned off in the event the production line stops. Conversely, the line should stop if the lamp source is ever disabled. While LEDs operate at much lower temperatures than conventional UV lamps, there is still enough energy (especially for webs and parts located very close to the light source) that prolonged exposure to a stationary heat-sensitive part can cause damage or break a web. Since LEDs can be turned off and on instantaneously, this safeguard is a painless alternative to damaged parts or equipment.
Shielding
Shielding refers to adding barriers to presses and material handling equipment in order to block stray or reflected light from application equipment and workers in close vicinity. Broadband sources contain shorter UVC and UVB rays that are potentially harmful to the body and also invisible. Longer UVA and UVV wavelengths are less of a medical concern but are extremely bright and unpleasant to the eyes. Integrators and press OEMs often use tinted plastics, sheet metal, and louvers to block the rays completely or reduce the brightness. For shorter wavelengths, this is necessary for safety reasons. For longer wavelengths this is done more fore operator and worker comfort. Shielding is also done to prevent UV rays from contacting critical or heat sensitive machine components, open formulation reservoirs, and material dispensing equipment.